Some parts with complex shapes or materials that are difficult to deform,
Traditional craftsmanship is difficult or even impossible to process,
It can be processed by spinning method,
Such as pulleys, lighting accessories, etc..
The utilization rate of spinning materials is high, and the mold cost is less than one-fifth of the stamping mold.
The tolerance of spinning is very small and can reach about IT8, the surface roughness is less than 3.2, and the strength and hardness are significantly improved.
(1) The metal stamping parts are made by punching under the premise that the raw material consumption is not large. The parts are lighter in weight and have good bending rigidity. After the plastic deformation of the plate, the internal organizational structure of the metal material is improved. Gradually increase the compressive strength of metal stamping parts.
(2) The metal stamping parts have high specification precision, are symmetrical with the mold parts, and have good tolerances. General installation and application regulations can be achieved without further machining.
(3) During the whole stamping process of infrared quartz heating tube Factory metal stamping parts, because the surface of the raw material will not be damaged, it has a good surface quality, and the appearance is smooth and beautiful, which provides a convenient standard for surface spraying, electroplating process, and other surface solutions.
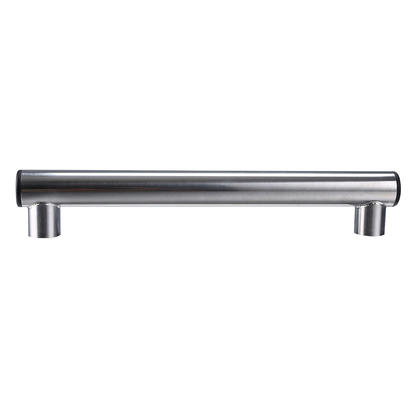
Composite mold: Common composite mold structures include composite blanking, composite stretching, etc. This mold structure is slightly different from other engineering mold structures. The punch (also known as male die or punch) is designed in the lower die, and the other templates are the lower splint (fixed punch punch), the lower stop plate and the lower stripper (outside), and the upper die in turn. It is composed of a master mold (or knife edge), an inner stripping plate and an upper backing plate. The inner stripping is hung on the upper backing plate by using an equal-height sleeve, and then it is supported by a rod or a spring. For example, for the composite mold used for blanking, the internal release is generally 0.50mm from the master mold, and it cannot be lower than the master mold, otherwise the knife edge of the master mold will easily collapse or not fall off.
Engineering die: Also known as "single-process die", it refers to a die that can only complete one stamping process in one stroke of stamping. After this project is finished, the product needs to be taken out of the mold manually or by a manipulator, and then placed in the mold of the next station to continue production, until one process of the mold is completed, the whole product is not completed. This kind of mold is simple to maintain, but it is time-consuming and labor-intensive to produce, requires more labor and time costs, and has a high product scrap rate.
Continuous die: Also known as "progressive die", it refers to a die that simultaneously completes two or more stamping processes at different stations during one stroke of stamping. This kind of die is difficult to maintain and requires experience A wealth of fitter masters operate, but the production efficiency is very high. If the speed is fast, thousands of products can be produced in one hour, saving labor and time costs.